Please note: James' blog has moved to a Wordpress site. To access it, please visit
http://jameswiebe.wordpress.com/. All posts have been transferred to the new site, and all new posts will only be accessible via Wordpress. Thank you for your interest!
Aerodynamic Tail Feather construction for a Belite
We'll cover both pieces of our horizontal tail assembly in this document: the elevator, and the horizontal stabilizer.
Construction of both pieces is very similar. Please refer to the blue prints for layout dimensional information.
Prior to assembly, all wood pieces are sanded and deburred. Steel and aluminum pieces are cleaned. Steel pieces are also painted, except where glue joints will be. (We cover the steel pieces with strategically placed masking tape, then spray paint is applied.)
Let's start with the elevator. We use 3M 2216 glue to attach the wood ribs to the elevator spar. We also glue tail end gussets to the end of each rib using high quality wood glue.
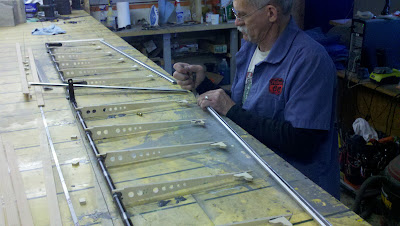 |
Elevator Assembly already under way. |
The trailing edge is fitted into place. It will fit snugly over the wood ribs and gussets. The trailing edge usually has a plastic film both inside and outside; remove the film.
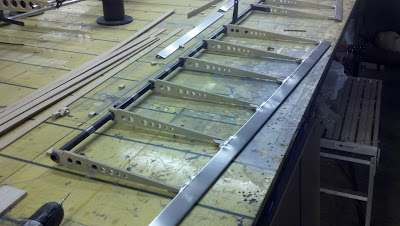 |
Trailing edge being fitted over elevator. |
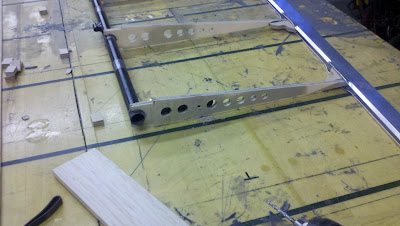 |
Still checking fit of trailing edge. |
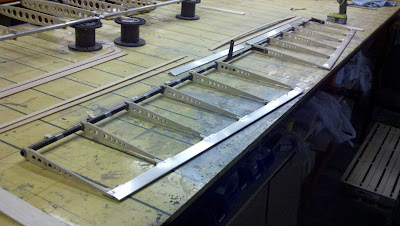 |
Trailing edge cut to length. |
Now it is time to install the four bolts, one on each torque arm.
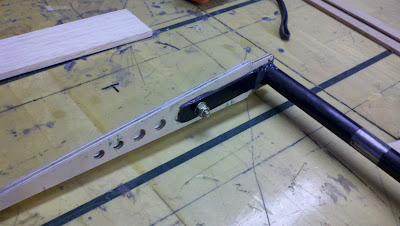 |
Bolts added. |
Use rivets to hold the trailing edge in place. Rivet washers are also used on the underside.
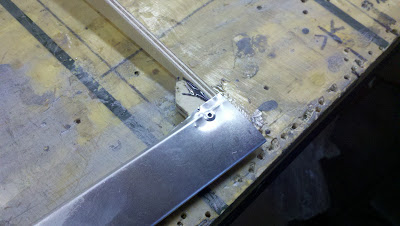 |
Trailing edge riveted in place. |
The wood strips are prepared by gluing in spacer blocks.
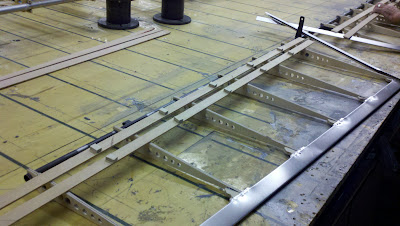 |
Wood strips and spacer blocks, glued together. |
The wood strips are then glued to the wood ribs.
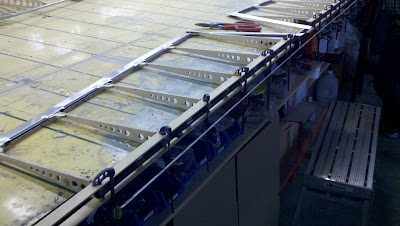 |
Wood strips glued to wood ribs. |
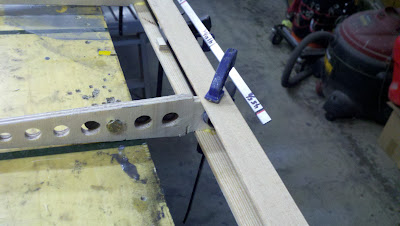 |
Closeup of clamping detail. |
Two pieces of trailing edge material are cut to fit in the center section.
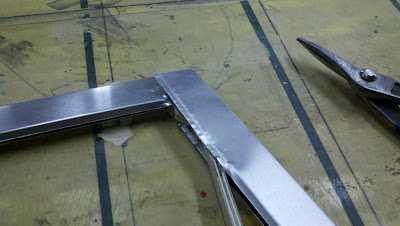 |
Preparing the center section trailing edge. |
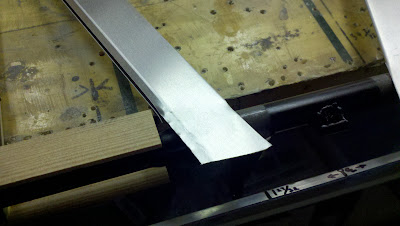 |
More preparation. |
Glue the balsa block on each end. Make room for the top of the bolt. Also, unlike shown below, it may be helpful to pretrim the outline of the rib in the balsa.